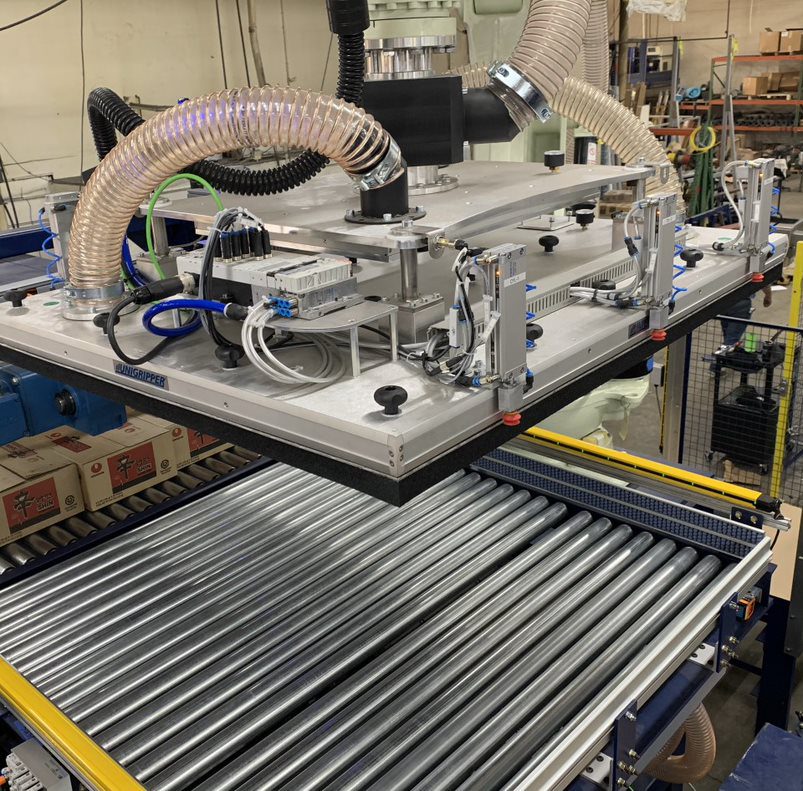
There are many advantages to automating your packaging lines. In most cases, automation allows you to package your product more consistently with fewer resources.
This is the perfect solution for the many plants struggling through labor shortages, or trying to retain reliable employees. Automation doesn’t eliminate your workforce, but it’s a huge opportunity for you to become more efficient.
In some cases, you can run a fully automated packaging line with one person. There are many companies out there still running their lines manually, and they might require four people just to bag, and then another two to palletize. In the long run, this is actually costing your company more money than you might think it’s saving you in the short term.
Automating your Packaging Lines based on Order Volume
Let’s go through an example.
Food & Beverage Company XYZ is growing like a weed. It went from being in a few local stores to now trying to fulfill purchase orders from grocery conglomerates like Target, Walmart, and Whole Foods. Prior to gaining purchase orders from the big grocery chains the manual process worked just fine and didn’t make sense to automate based on lack of volume.
Now, they certainly have the volume to support automation. Their current process of three people on the bagging line and two people palletizing at the end of the line just isn’t working. They can’t get enough people to work on the lines and when they do the product is inconsistent. If they can’t fulfill orders to the big grocery chains it’s going to be detrimental to their growth.
Solving for the Blue Collar Labor Shortage
Enter automation.
A fully automated packaging line will cost them roughly $1 million and they expect to see a return on their investment in just 18 months. How did they do this?
By working smarter, not harder.
The plant manager and leadership team decided to invest their money into a system to support their volume rather than investing countless time finding, training, and retaining new employees. In addition to their monetary investment, they also committed to increasing their salaries to attract more qualified employees who will stick around longer due to the much improved working environment. Instead of six employees to run the line, they now have one or two for each shift.
How to Hire the Right People to Run Automated Packaging Lines
It’s no secret there is a shortage of blue-collar workers right now. Working long hours in labor intensive jobs certainly takes a toll on people. Oftentimes people jump around for either more money, or a better working environment. Automation helps you solve for both.
You need an experienced person who is detail oriented and has laser focus. This person also needs to have great communication skills. Machines go down. It’s not if, but when. The right person needs to have a great working relationship with your maintenance technicians, plant manager, and automation partner. These open lines of communication help identify smaller problems before they become much larger ones.
Potential Benefits of Promoting from Within your Plant
In many cases, this person might already be in your plant. When making the switch to automation someone needs to clearly articulate the current packaging process, and identify key considerations. Oftentimes, the best person to get this information from is someone who has experience with the current process.
It’s important to let your current workforce know you’re not looking to replace them – especially the workers you want to keep in the transition. Let them know you’re moving to automation to make their lives easier. In addition to saving their backs from 10 hours of consecutive palletizing, you also plan to move them to a different portion of the plant, or pay them more to be the keeper of the automated line. They will certainly appreciate knowing their job isn’t in danger up front, and will be more willing to communicate consideration to you and your automation partner.
Don’t Replace Jobs. Make Them Better
We’ve written about this before. Automation doesn’t eliminate jobs. It makes them better.
Moving to automation is certainly an opportunity to increase your production at a more consistent and scalable rate. However, it’s also a great opportunity for your current workforce to take advantage of new and important roles within your plant.
Find someone who will show up to work everyday, is great at working with other people within the plant, and has excellent critical thinking skills and your lines will run smooth as ever.
NOVA Automation is Happy to Help
We pride ourselves on being consultative in our approach. Your success is our success. If you’re struggling to decide whether or not automation makes sense for your plant, or are trying to figure out what resources are needed to support automation just let us know. We’d love to talk through potential solutions.