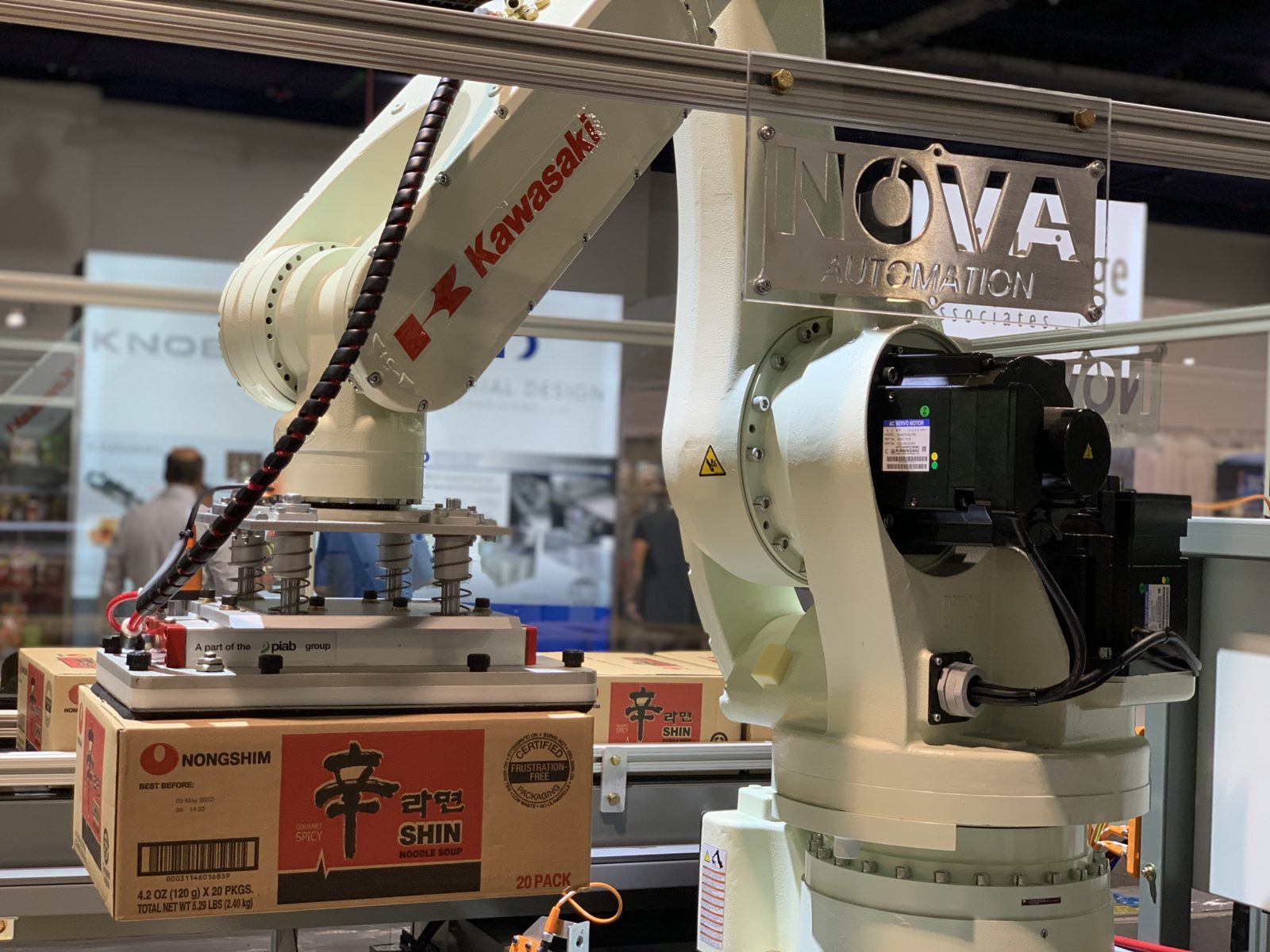
Automation is a great way to package more product without necessarily adding more people to your workforce. For most companies, the most logical place to start with automation is at the end of the packaging line.
Manual palletizing requires multiple people at the end of your line performing repetitive tasks. It can also be physically demanding depending on the weight of the cases you are palletizing.
Stacking 25 lbs. cases for eight hours or more each day isn’t fun for anyone, and oftentimes the end product suffers.
Common themes from companies manually palletizing product
- It’s hard to find human labor
- Once they find workers they are unreliable because it’s so demanding physically
- Pallets are messy
- Slow rates
- Having to stop and start the lines multiple times per day
The list of issues with manual palletizing goes on and on.
Reasons why companies are still manually palletizing product
- It’s the way they’ve always done it (If it’s not broke why try and fix it?)
- They don’t have the volume to support automation from an ROI perspective
- Leadership doesn’t understand (or want to understand) automation
- They’ve had a previous bad experience with automation
- They don’t have the space for packaging automation equipment
Experimenting with potential opportunity when you have a good thing going might seem like an unnecessary risk. Are you leaving potential revenue on the table by producing at your current rate?
If you don’t have enough volume there is no point in waiting years and years to hopefully see a return on your investment for replacing manual labor.
We certainly run into senior executives who still think automation is just a fad, or have had a bad experience with automation from another project or vendor.
The most common objection we hear is companies just don’t have enough floor space to bring in the equipment needed to automate their production lines.
We hear you. The whole industrial automation industry heard you as well.
While walking the halls of Pack Expo we noticed more and more small footprint robotic solutions. It can be overwhelming to decide which one is right for you and your plant.
Evaluating Small Footprint Automation Equipment
NOVA Automation’s version of the small footprint robotic palletizing cell is our mobile palletizing cell. The MPC-80 robotic palletizer has the latest robotic technology and is designed to support payloads up to 80 kg and is ready to palletize on delivery. Åll you have to do is place the palletizing cell where you’d like it, add industrial power, connect to compressed air, and you’re all set.
Here’s a complete list of features and benefits:
- Ready to palletize on delivery
- No Install Required
- Place the palletizing cell with a forklift, add power, connect to compressed air, and you’re all set
- System includes NOVA’s safety zone scanner to provide interaction with operators during continuous operations
- Comes standard with NOVA’s advance control system and pallet builder software, allowing your operators to design new patterns in minutes
- Available in 30, 50, 80 kg payload robots
- Option to palletize on both sides of the cell for increased efficiency
- Smaller, more mobile footprint than a conventional palletizer, allowing you to easily relocate within your plant if needed
What’s the difference between a mobile palletizing cell and a collaborative robot?
The main difference between cobot models and a mobile palletizing cell is the safety limitations imposed by the cobot or robot. They’re called cobots for a reason. They are designed to run with the presence of humans.
The biggest advantage to the mobile palletizing cell is you get all of the benefits of cobots with increased rates, higher payloads, and better reliability
Both the mobile palletizing cell and cobots are equipped with safety sensors designed to prevent injury to those interacting with the cell. The mobile palletizing cell palletizes on its own, so it’s enclosed within safety fencing and has a sensor designed to either slow or stop depending on how close someone is to the cell.
Both are easy to use and easy to program. Our mobile palletizing cell comes with our advanced NOVA controls system and easy to use pallet builder. Like a cobot, it doesn’t require extensive coding knowledge, or someone to come out and reprogram.
The light duty nature of a cobot is both a blessing and a curse in many cases. It’s easy to move to different areas of your plant. The mobile palletizing cell can be moved easily with a forklift.
The mobile palletizing cell can be moved from line to line and quickly programmed for new pallet configuration.
The Bottom Line when Evaluating Small Footprint Robotic Palletizing Equipment
Both the mobile palletizing cell and cobot solutions can make the lives of your end of line employees much easier and have similar footprints.
Cobots are your choice if:
1. Extremely light payloads
2. Slow Rates
3. You’re not worried about potential downtime, or longevity
Mobile Palletizing Cell is your choice if:
1. You need to maintain production level rates above six cases per minute
2. Your cases are up to 150 lbs.
3. You’re packaging product in a more challenging environment such as temperatures below freezing
Let the Robotic Palletizing Experts at NOVA Automation Help
The way to find the best solution is to work closely with an integrator, or manufacturer. This relationship should start out as consultative to ensure success for both parties. The integrator can work closely with you to make sure the solution recommended checks all of the boxes you need checked to be successful.
If you’re considering automating the end of your packaging line, but aren’t sure which option works best for you, contact us today. We have been helping companies package more product for more than 25 years and would love to help guide you through the automation process.